5 simple steps to create an SOP plan.
- Anco Equipment
- Mar 3
- 2 min read
Updated: Mar 10
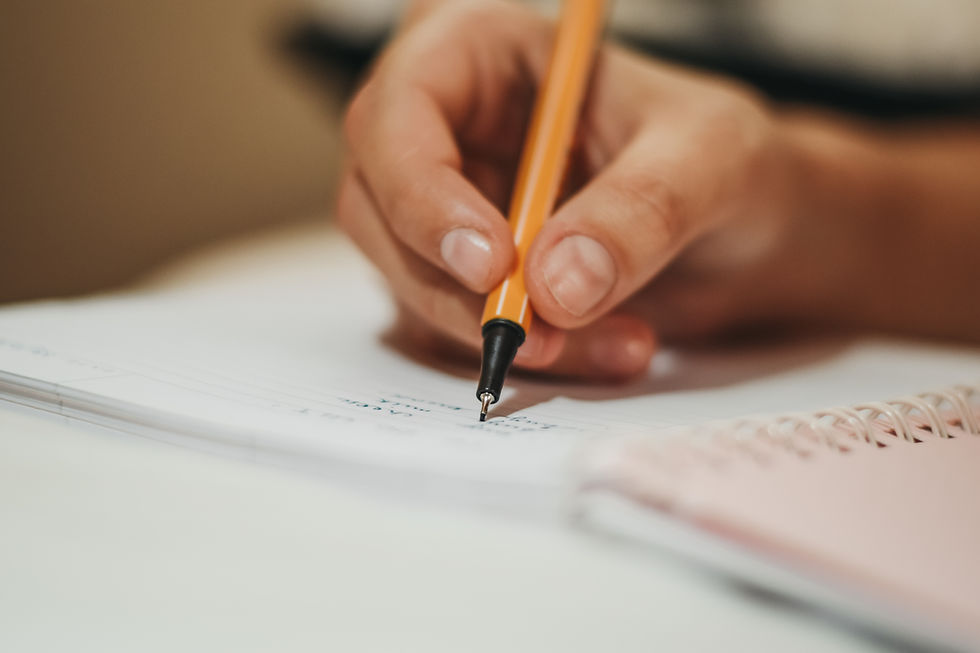
In the face of these challenges, developing a Standard Operational Plan (SOP) might appear overwhelming, even when its advantages are well-recognized and documented. An SOP can streamline operations, boost efficiency, and ensure uniformity, making it an essential asset for any production facility. However, the prospect of drafting an SOP can be daunting, as it demands a comprehensive understanding of current operations, areas for enhancement, and the ability to effectively communicate these procedures to all staff. To ease this process, here are five simple steps to crafting a thorough SOP plan that can help reduce some of the challenges associated with managing a production facility:
Define the Purpose and Scope: Whether it involves operating your cosmetic processing equipment or cleaning a dairy mixing tank, start by clearly outlining what the SOP aims to achieve. Identify the specific processes or tasks requiring standardization and set the objectives of the SOP. This step will provide clear guidance and ensure all stakeholders recognize the document's significance.
Collect Input from Key Stakeholders: Engage employees directly involved in the processes being documented. Their insights and experiences are crucial for identifying best practices and potential issues. Consider creating a simple video of the process. This allows employees to learn visually and audibly, and you can draft your text from it to ensure the SOP accurately reflects workplace realities.
Compose the SOP Document: Begin writing the SOP by organizing the information logically. Use clear and concise language, breaking down the processes into manageable steps. Include necessary details such as roles and responsibilities, safety protocols, and any required tools or materials. For instance, if your plan involves the procedure for cleaning commercial food processing equipment, ensure you follow the cleaning chemicals manufacturer's instructions. Visual aids like flowcharts or diagrams can enhance understanding and retention.
Review and Revise: After completing the initial draft, share it with employee operators for feedback. This collaborative review process is vital for identifying any gaps or unclear instructions. Make necessary revisions based on the feedback received, ensuring the final document is comprehensive and user-friendly.
Implement and Train: Once the SOP is finalized, implement it throughout the facility. Conduct training sessions to acquaint employees with the new procedures, highlighting the importance of adhering to the SOP for their safety and product quality. Regularly revisit the SOP to ensure it stays relevant and effective, updating it as needed based on process changes or staff feedback.
By following these steps, production facility owners and project managers can establish an effective Standard Operational Plan that not only boosts operational efficiency but also fosters a safer and more productive work environment. This structured approach can ultimately lead to improved employee morale, higher quality products, and a more profitable business overall.
Comments